11 Powerful Tips for Perfect Shuttering and Shuttering Learn all about Shuttering and Shuttering: types, tools, cost, defects, and expert tips for safe and quality concrete formwork in the USA.
Table of Contents
11 Expert Tips & Facts About Shuttering and Shuttering is a critical part of every concrete construction project. It involves setting up temporary molds that hold the concrete in place until it hardens and gains sufficient strength. From residential slabs to multi-story columns, shuttering plays a vital role in shaping and supporting structural elements. In this detailed guide, we explore the types, materials, tools, IS codes, and professional tips to help you execute shuttering work efficiently and safely, especially for U.S. construction projects Shuttering and Shuttering.
- Temporary mold for shaping concrete.
- Essential for RCC components like beams and columns.
- Timber: Traditional, reusable with care.
- Steel: Durable and precise.
- Plastic/Aluminum: Lightweight, corrosion-resistant.
- Sheathing, battens, supports, and bracing.
- All work together to contain wet concrete.
- Shuttering: Vertical surfaces β columns/walls.
- Centering: Horizontal surfaces β slabs/beams.
- Material planning, fixing, alignment, and removal.
- Emphasize safety and accuracy at all stages.
- Columns: 16β24 hrs
- Beams: 7 days
- Slabs: 14 days
- IS 456:2000 β RCC Practice.
- IS 14687 β Shuttering Material Guide.
- Form oil, clamps, props, vibrators, measuring tools.
- Vital for clean finishes and safety.
- Costs vary by material, complexity, area.
- Use local labor wisely for savings.
- Timber: Limited reuse, biodegradable.
- Steel/Plastic: Highly reusable, recyclable.
- Prevent honeycombs, bulges with proper bracing.
- Apply release agents to reduce sticking.
- Ensure perfect level and plumb.
- Use clean and undamaged materials.
What Is Shuttering? Tips for Shuttering and Shuttering
Shuttering and Shuttering refers to the temporary mold or framework used to hold wet concrete in place until it gains enough strength to support itself. This essential process in construction is critical for shaping various structural elements such as columns, beams, slabs, and retaining walls. Shuttering is a vital part of formwork, and its precision directly affects the strength, shape, and finish of the concrete structure.
In Reinforced Cement Concrete (RCC) construction, shuttering ensures that concrete is formed with accurate dimensions and smooth surfaces. Without proper shuttering, the concrete can bulge or leak, leading to structural defects such as honeycombing or weak joints.
Contractors select different shuttering systems based on project needs, budget, and the complexity of the design. For example, smaller residential projects may use timber, while large commercial buildings prefer steel or aluminum shuttering for durability and multiple reuse cycles.
Apart from shape and support, shuttering also ensures safety on site. If poorly installed, it can collapse during concrete pouring, risking injuries and major structural flaws. Therefore, formwork engineering and skilled labor are essential to achieve quality construction.
In summary, understanding the basics of Shuttering and Shuttering helps builders ensure strength, durability, and efficiency in concrete construction. Itβs more than just a mold itβs the backbone of any well built RCC structure.
Types of Shuttering Materials
Choosing the right material is essential for effective Shuttering and Shuttering work. The performance, cost, durability, and finish of concrete elements depend heavily on the shuttering material used. Letβs explore the most common types and where theyβre used:
1. Timber Shuttering
Timber is the most traditional and widely used formwork material. Itβs especially common in small residential or low-rise construction. Itβs lightweight, easy to cut into custom shapes, and relatively affordable. However, it is less durable and reusable compared to other materials. Timber must be properly seasoned and treated to resist moisture and warping. For budget-conscious projects, timber remains a practical choice.
2. Steel Shuttering
Steel is durable, provides excellent alignment, and delivers a smooth finish to concrete surfaces. Itβs ideal for high-rise buildings, bridges, and large commercial structures. Although it requires a higher initial investment, it pays off in the long term due to its high reusability (up to 100 times). Itβs resistant to warping, shrinkage, and moisture, which makes it a top choice for professional construction firms.
3. Aluminum and Plastic Shuttering
Aluminum shuttering is lightweight yet strong, making it suitable for repetitive and large-scale construction. Itβs particularly popular in modular systems and housing schemes. Plastic shuttering, often made from polymer-based sheets or panels, is corrosion-resistant, easy to clean, and suitable for simple structures like driveways and sidewalks.
Each material has its strengths, and selection should be based on project size, complexity, budget, and required surface finish. For environmentally conscious projects, steel and plastic shuttering offer sustainable reuse options.
To ensure quality in Shuttering and Shuttering, always match the material with structural needs, labor skill level, and environmental conditions. Proper handling and storage also increase the lifespan and efficiency of the shuttering system.
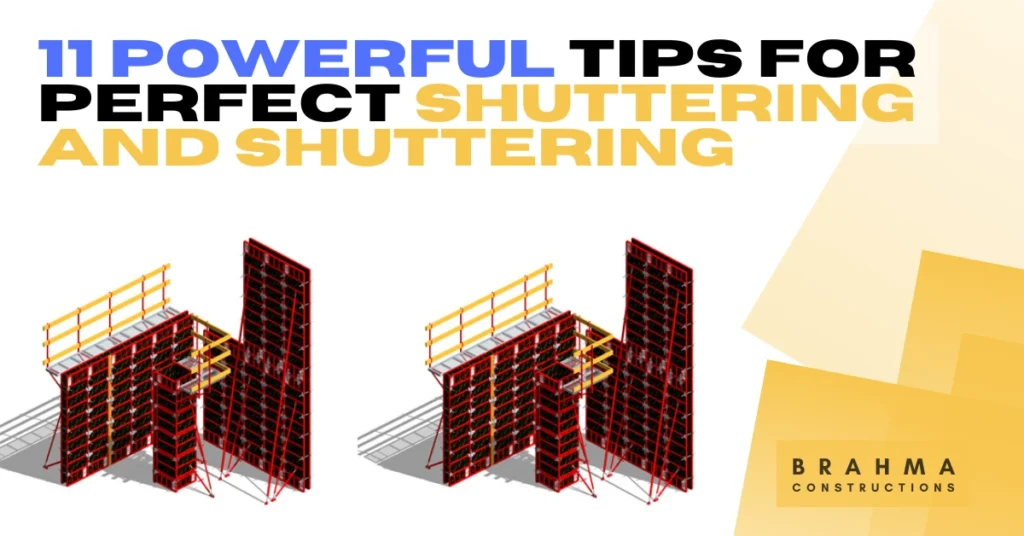
Components of a Shuttering System
A proper Shuttering and Shuttering setup is made up of several key components that work together to hold wet concrete in the desired shape and position. Understanding these components helps ensure structural safety and precision in concrete works, especially in RCC (Reinforced Cement Concrete) structures.
1. Sheathing (Form Face)
This is the surface that comes in direct contact with wet concrete. It forms the actual shape of the structure. The sheathing must be smooth, waterproof, and strong enough to bear the pressure of fresh concrete. Materials used include plywood, steel, or plastic.
2. Battens (Joists and Panels)
Battens are horizontal members that support the sheathing. They transfer the load from the sheathing to the props and provide rigidity. Properly spaced battens prevent sagging and deformation of the mold during the pouring process Shuttering and Shuttering.
3. Props and Supports
These vertical components, such as steel pipes, wooden posts, or adjustable jacks, bear the load of the shuttering system and the weight of wet concrete. They hold the framework in position until the concrete gains enough strength.
4. Bracing and Tie Rods
Bracing offers lateral stability, preventing buckling or shifting. Tie rods, bolts, and clamps hold the framework together tightly, ensuring it stays aligned and doesnβt bulge or leak during concrete pouring.
Each part plays a vital role in the integrity of the formwork. Shuttering and Shuttering Missing or poorly installed components can lead to shuttering failure, which may cause serious safety issues or structural defects.
In every Shuttering and Shuttering project, a well-coordinated system of sheathing, battens, props, and bracing ensures that concrete is poured safely, cures properly, and achieves the desired finish. The strength and quality of your structure begin with how well the shuttering is assembled.
Components of a Shuttering System
A proper Shuttering and Shuttering setup is made up of several key components that work together to hold wet concrete in the desired shape and position. Understanding these components helps ensure structural safety and precision in concrete works, especially in RCC (Reinforced Cement Concrete) structures.
1. Sheathing (Form Face)
This is the surface that comes in direct contact with wet concrete. It forms the actual shape of the structure. The sheathing must be smooth, waterproof, and strong enough to bear the pressure of fresh concrete. Materials used include plywood, steel, or plastic.
2. Battens (Joists and Panels)
Battens are horizontal members that support the sheathing. They transfer the load from the sheathing to the props and provide rigidity. Properly spaced battens prevent sagging and deformation of the mold during the pouring process.
3. Props and Supports
These vertical components, such as steel pipes, wooden posts, or adjustable jacks, bear the load of the shuttering system and the weight of wet concrete. They hold the framework in position until the concrete gains enough strength.
4. Bracing and Tie Rods
Bracing offers lateral stability, preventing buckling or shifting. Tie rods, bolts, and clamps hold the framework together tightly, ensuring it stays aligned and doesnβt bulge or leak during concrete pouring.
Each part plays a vital role in the integrity of the formwork. Missing or poorly installed components can lead to shuttering failure, which may cause serious safety issues or structural defects Shuttering and Shuttering.
In every Shuttering and Shuttering project, a well-coordinated system of sheathing, battens, props, and bracing ensures that concrete is poured safely, cures properly, and achieves the desired finish. The strength and quality of your structure begin with how well the shuttering is assembled.
Process of Shuttering Work on Site
A well-executed Shuttering and Shuttering process is the foundation of strong and dimensionally accurate concrete structures. From planning to removal, each stage requires careful execution to maintain quality and safety on site. Below is a step-by-step outline of how shuttering is done:
1. Planning and Layout
The process begins with reading structural drawings and planning the shuttering layout. Engineers assess the dimensions, load requirements, and shape of the concrete member. Based on this, they choose appropriate shuttering materials and formwork types.
2. Material Preparation
Once the layout is finalized, all shuttering materials like sheathing, props, clamps, and bracing are brought to the site. These materials are checked for cleanliness, structural strength, and alignment. Form release agents are also applied to prevent concrete from sticking to the mold.
3. Fixing the Shuttering
The formwork is assembled and fixed in place based on the planned layout. Vertical or horizontal supports (depending on whether itβs shuttering or centering) are installed securely. Alignment tools like plumb bobs, spirit levels, and laser levels are used to ensure proper positioning.
4. Reinforcement Check
Before pouring concrete, reinforcement is placed inside the shuttering. Clear cover spacing and bar placement are double-checked to avoid corrosion or structural failure later.
5. Concreting and Vibration
Concrete is poured into the shuttered form and compacted using needle vibrators to eliminate air pockets. This helps in avoiding honeycombing and improves the concrete’s strength and finish.
6. Curing and Removal (Deshuttering)
After a specific curing period (based on IS codes), the shuttering is carefully removed without damaging the structure. Reusable materials are cleaned and stored for future use.
Every Shuttering and Shuttering operation must follow safety protocols and quality checks at each step. Shuttering and Shuttering This ensures the integrity of the concrete work and avoids costly repairs or accidents.
Stripping Time for Shuttering
Stripping time refers to the duration after which shuttering can be safely removed without compromising the strength and shape of the concrete. In any Shuttering and Shuttering project, following the correct stripping times is crucial to avoid surface damage, sagging, or even collapse. These timelines vary based on the concrete element, weather, and materials used.
Standard Stripping Times
1. Vertical Formwork (Columns, Walls): 16 to 24 Hours
For vertical structures, formwork can usually be removed after 16β24 hours, provided the concrete has gained enough strength to support itself. However, the forms should only be taken off once edges can bear light pressure without crumbling.
2. Slabs (Props Left Under): 3 Days
If youβre not removing the props (supporting elements), slab formwork can be stripped after 3 days. The props ensure that the slab does not deflect under its own weight or other construction loads.
3. Beam Soffits (Props Left Under): 7 Days
The bottom surface of beams (soffits) can have their formwork removed after a week, as long as props remain to support the weight. Beams take longer to cure and gain strength due to their depth.
4. Full Removal (Slabs and Beams): 14 to 21 Days
If props are to be removed entirely, wait at least 14 days for slabs and 21 days for beams. This allows concrete to reach adequate compressive strength.
Key Note:
Always adjust times depending on temperature, humidity, and concrete mix. Cold conditions may require longer curing, while high-performance concrete may allow earlier stripping.
Following proper stripping times in Shuttering and Shuttering not only protects structural safety but also ensures a better surface finish and longevity of the concrete.
π§° Tools and Equipment Used in Shuttering
Efficient and safe Shuttering and Shuttering work requires the right set of tools and equipment. These tools help in assembling, aligning, and disassembling the formwork system while ensuring concrete is cast to high quality standards. Using proper tools not only speeds up the work but also minimizes errors and defects.
1. Formwork Oil (Release Agent)
This is applied to the surface of formwork to prevent concrete from sticking. It allows for easy removal of shuttering without damaging the surface finish. Using high-quality oil also increases the reusability of formwork materials like plywood and steel.
2. Clamps and Tie Rods
These hold the shuttering panels tightly in place. Clamps maintain pressure between adjoining panels, while tie rods pass through formwork walls to prevent bulging from concrete pressure. Without these, formwork may open up during pouring, causing leakage and misalignment.
3. Adjustable Jacks and Props
Used mainly in centering (horizontal shuttering), these adjustable supports hold slabs, beams, and floors in position. They are designed to handle heavy loads and can be adjusted for height, ensuring proper leveling.
4. Needle Vibrators
These are inserted into freshly poured concrete to remove air bubbles and ensure a compact, uniform structure. This helps in avoiding honeycombing, which is a common defect in Shuttering and Shuttering works.
5. Measuring Tools
Plumb bobs, spirit levels, and laser levels help ensure that shuttering is straight, level, and aligned correctly. Proper measurement avoids tilt or uneven thickness in structural elements.
Using these tools ensures high accuracy and durability in any Shuttering and Shuttering application. Investing in good-quality equipment and training workers on their use will significantly enhance the overall quality of your RCC structures.
Cost and Labor Involved in Shuttering and Shuttering
When planning a construction project in the U.S., understanding the cost and labor associated with Shuttering and Shuttering is essential for staying on budget. Whether you’re building a residential deck or a commercial structure, formwork costs can represent up to 20β25% of total concrete work so knowing the cost drivers makes a big difference.
1. Factors That Influence Cost
- Material Type: Timber is still used for small-scale or custom projects, while steel and aluminum formwork systems are common in commercial jobs due to durability and reusability.
- Project Size & Complexity: A simple slab for a driveway costs far less than formwork for multilevel columns or retaining walls.
- Labor Rates: In the U.S., hourly labor costs for formwork carpenters range from $25 to $45/hour depending on experience, state, and union affiliations.
- Region: Construction costs in California or New York will be higher than in states like Texas or Florida due to labor demand and local regulations.
2. Typical Pricing (2025 Estimates)
- Timber Shuttering: $2β$5 per square foot.
- Steel Formwork: $5β$8 per square foot (higher upfront, but reusable).
- Modular Formwork Systems (e.g., PERI, Doka): Can cost more initially but offer speed and precision for large-scale construction.
3. Cost-Saving Tips
- Reuse shuttering materials when possible.
- Rent formwork systems from local suppliers if buying isnβt viable.
- Optimize labor with pre-planning and correct alignment to avoid rework.
For U.S.-based builders, investing in the right tools, trained labor, and proper formwork planning leads to safer structures and significant savings. Smart budgeting in Shuttering and Shuttering ensures quality without blowing your construction budget.
Reusability and Environmental Impact of Shuttering and Shuttering
In modern construction especially in the U.S. sustainability and cost-efficiency are key concerns. Thatβs why evaluating the reusability and environmental impact of materials used in Shuttering and Shuttering has become more important than ever. By choosing eco-friendly and reusable formwork, you not only reduce your projectβs carbon footprint but also save on recurring costs.
1. Timber Shuttering
- Reusability: Can typically be reused 5 to 10 times, depending on the quality and care taken during removal and storage.
- Environmental Impact: Timber is biodegradable and renewable if sourced sustainably. However, using low-grade wood or overusing trees without replantation harms forests.
- Tip: Choose FSC-certified timber and apply form-release agents to extend its usability.
2. Steel and Aluminum Shuttering
- Reusability: Extremely high steel formwork can be reused 100+ times, and aluminum slightly more if properly maintained.
- Environmental Impact: Though manufacturing steel/aluminum involves high energy, their recyclability makes them eco-friendly long-term. Plus, fewer replacements reduce landfill waste.
- Best For: Large commercial projects, bridges, and repeat slab/casting jobs.
3. Plastic Formwork
- Reusability: Often lasts for 40β50 uses, and is resistant to corrosion and water damage.
- Environmental Impact: Made from polypropylene, which is recyclable, though not biodegradable. Still, it’s a good middle-ground for affordability and sustainability.
4. Smart Practices for Greener Formwork
- Rent instead of buying, especially for one-time use.
- Use form release agents to protect form faces and avoid sticking.
- Store materials properly to prevent early wear or weather damage.
For construction professionals in the USA, embracing eco-conscious Shuttering and Shuttering methods doesnβt just help the environment it builds long-term savings and a reputation for responsible building.
Common Shuttering Defects and How to Avoid Them
Even with the best materials and planning, Shuttering and Shuttering can lead to construction defects if not executed properly. These issues not only affect the appearance of the concrete but can also compromise structural integrity. Below are the most common shuttering problems seen on U.S. construction sites plus expert tips to avoid them.
1. Honeycombing
This defect appears as small air gaps or holes on the concrete surface due to poor compaction. It weakens the structure and creates an entry point for moisture, leading to corrosion.
How to Avoid:
- Use needle vibrators to compact concrete evenly.
- Ensure the formwork is well-sealed with no leak points.
- Avoid dry concrete mixes maintain proper water-cement ratio.
2. Bulging or Warping
This happens when the formwork cannot withstand the pressure of fresh concrete, causing it to bend outward. It leads to irregular shapes and uneven surfaces.
How to Avoid:
- Use proper bracing and tie rods.
- Select formwork material based on load requirements.
- Check alignments with plumb levels and laser tools before pouring.
3. Leakage of Cement Slurry
Cement slurry can leak through joints in poorly sealed shuttering, resulting in weak edges and poor finish.
How to Avoid:
- Apply form release oil evenly.
- Seal all joints tightly using foam strips or tape.
- Inspect for gaps before pouring concrete.
4. Misalignment
Improper positioning of formwork causes columns and beams to lean or tilt, leading to unsafe and unprofessional construction.
How to Avoid:
- Double-check placement using plumb bobs and spirit levels.
- Use templates or layout marks as guides.
By being aware of these common issues and implementing preventive measures, your Shuttering and Shuttering work can achieve a smooth, strong, and reliable finish while saving on costly repairs and delays.
Tips for Quality Shuttering Work
High-quality Shuttering and Shuttering work is essential for ensuring the strength, appearance, and durability of any concrete structure. Whether you’re working on a residential foundation or a large commercial slab in the USA, following some expert practices can greatly improve results and reduce defects.
1. Use Clean and Damage-Free Materials
Before starting, inspect all shuttering panels whether timber, steel, or plastic for cracks, warping, or residue from previous jobs. Clean surfaces ensure smooth concrete finishes and easy removal after curing.
Pro Tip: Apply formwork oil (release agent) evenly to all surfaces before pouring concrete. It prevents sticking and protects the formwork for reuse.
2. Ensure Proper Alignment and Levels
Use tools like laser levels, plumb bobs, and spirit levels to keep the shuttering aligned vertically and horizontally. Misalignment leads to tilted columns and uneven slabs, requiring costly rework.
On-Site Tip: Mark alignment guides on the slab or floor to help workers position shuttering panels correctly.
3. Secure the Shuttering System Firmly
Always double-check that clamps, tie rods, and supports are tightly fixed. If any section shifts during pouring, it could lead to bulging or formwork failure.
Pro Tip: Use steel props or adjustable jacks in high-load areas like beams and slabs to distribute weight evenly.
4. Maintain Correct Cover and Clearances
Check that the reinforcement has the correct spacing from the shuttering wall. This ensures the concrete has proper cover for durability and resistance to corrosion.
Tip: Use cover blocks approved under U.S. standards like ASTM.
5. Train and Supervise Labor
Many shuttering defects occur due to poor workmanship. Invest in skilled labor or train your crew in best practices, safety, and formwork techniques.
By following these tips, contractors and site engineers in the U.S. can achieve top-notch Shuttering and Shuttering results ensuring strong, safe, and beautiful concrete work on every project.
β FAQs: Shuttering and Shuttering
Q1: What is shuttering in construction?
Shuttering is the process of creating temporary molds to hold concrete in shape until it sets and gains strength. Itβs also called formwork.
Q2: What is the difference between shuttering and centering?
Shuttering refers to vertical formwork like walls and columns, while centering supports horizontal elements like slabs and beams.
Q3: How many times can shuttering be reused?
Timber can be reused 5β10 times, plastic around 40β50 times, and steel over 100 times, depending on maintenance.
Q4: How much does shuttering cost in the USA?
Costs vary from $2β$8 per square foot depending on the material, labor, and project complexity.
Q5: Which IS codes are relevant to shuttering work?
IS 456:2000, IS 14687, and IS 4990 are the most important standards for shuttering and formwork practices.
Buy the Best Rebar Bender in the USA
Learn all about Rebar Bender types, uses, prices, top brands, safety tips & buying guide. Perfect for builders, engineers & DIY projects.
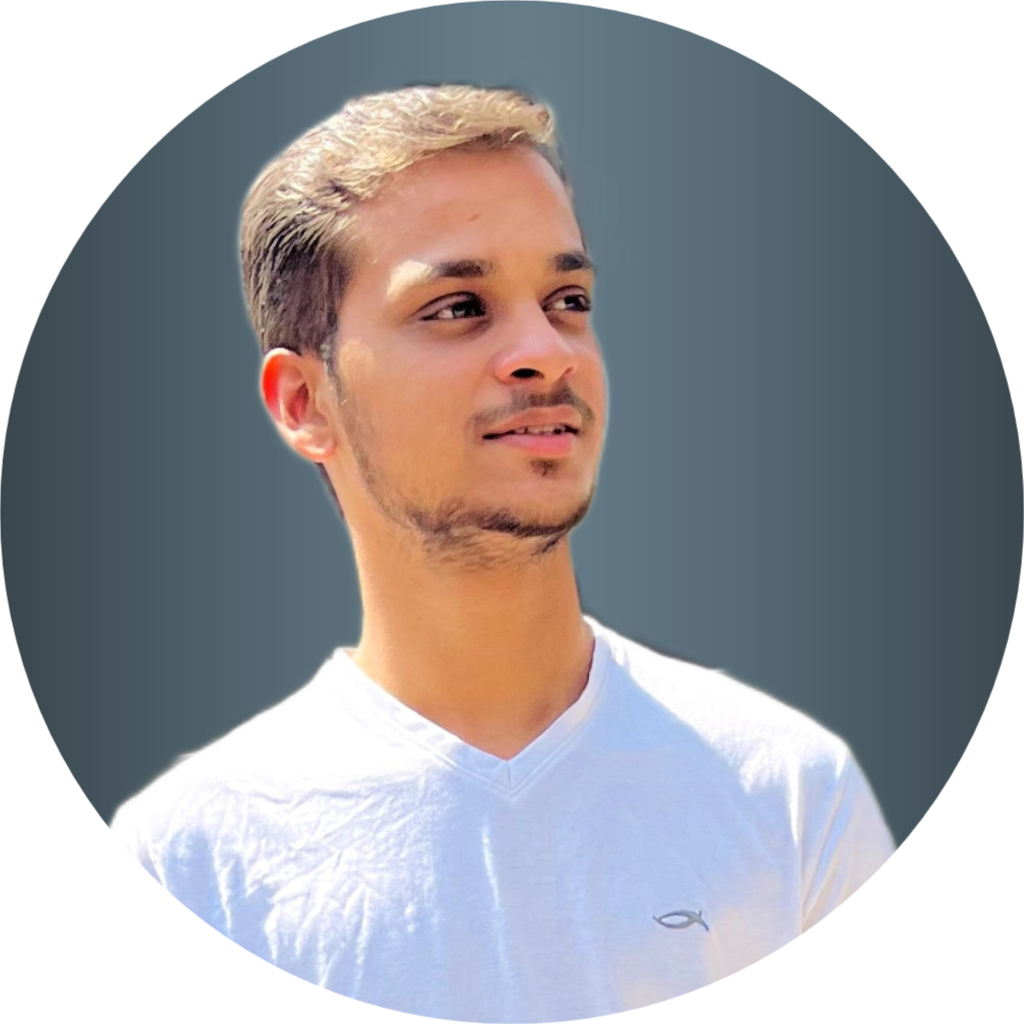
Hi, Iβm Sanskar Shinde β a civil engineer, blogger, and construction enthusiast. With 3 years of experience in the field, I love sharing real-world tips, project ideas, and practical knowledge through my blog, Brahma Constructions.